PE Transparent Ziplock Bag Logo Screen Printing Process Introduction
PE transparent ziplock bag is a plastic product widely used in the packaging field. By printing the logo or other patterns on the bag, it not only enhances the brand image of the product, but also plays the role of information transmission. Screen printing is the main printing method and is widely used because of its strong adaptability, bright colors and stable printing effect. The following will introduce the process difficulties, machines used, operation procedures and precautions.
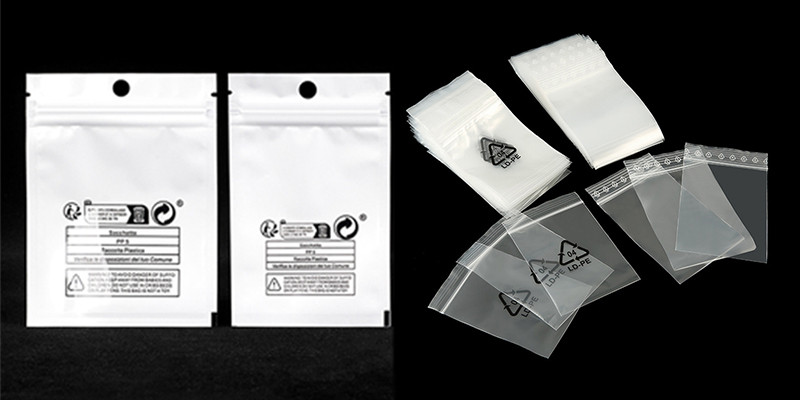
I. Process Difficulties :
1.Surface treatment requirements : PE material has low surface tension and poor adhesion when printed directly. It needs to be treated with corona or coating to increase the surface tension and ensure that the ink adheres firmly.
2.Ink selection : Special plastic screen printing ink should be used, taking into account flexibility, adhesion and environmental protection requirements.
3.Film deformation control : PE bags are thin and soft, and are easily deformed by pressure or temperature, which may cause pattern distortion.
4.Abrasion resistance and color fastness : The printed pattern is required to have certain abrasion resistance and anti-fading properties to ensure long-term use.
II. Equipment used :
1.Screen printing machine : Flat screen printing machine or roller printing machine is mostly used, which is suitable for the printing needs of thin film materials.
2.Corona treatment equipment : important equipment to increase the surface tension of PE and ensure the adhesion of ink.
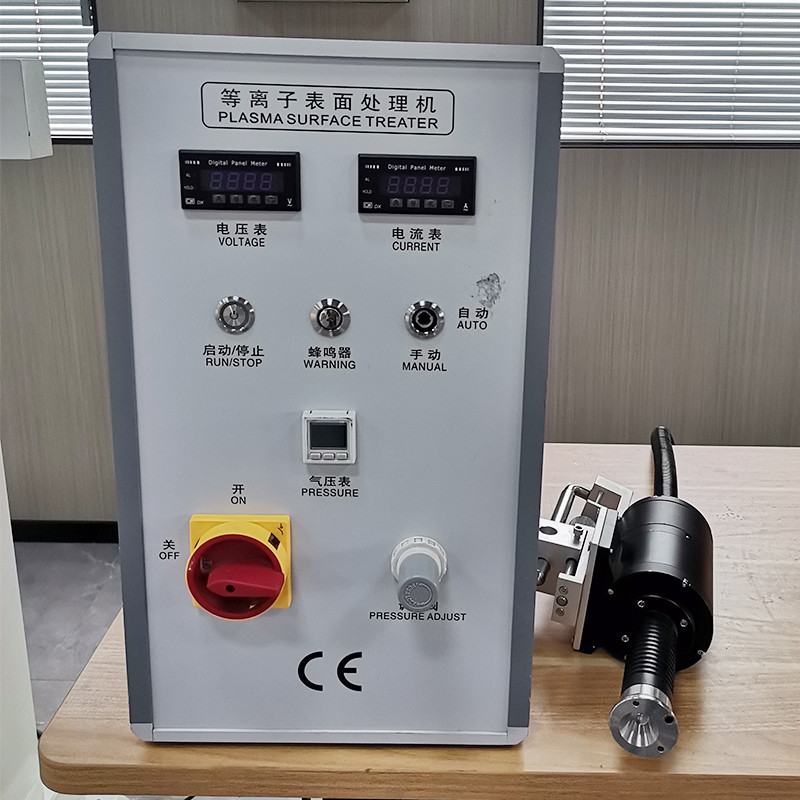
3.Drying equipment : such as infrared dryer or hot air dryer, used to quickly cure the ink.
III. Operation process :
1.Surface treatment :
The PE bag is subjected to corona treatment to increase the surface tension and its compliance value is tested (generally above 38 dynes).
2.Plate making and debugging :
Make screen plates according to the Logo design and adjust the printing machine parameters, including pressure, scraper angle, etc.
3.Ink mixing :
Mix ink according to color requirements to ensure moderate viscosity and avoid drawing or smudging during the printing process.4.Test printing and adjustment :
Carry out test printing to check whether the pattern is clear and the position is accurate, and make fine adjustments based on the actual effect.
5.Batch printing :
During the formal printing process, pay attention to keeping the speed stable to prevent the pattern from shifting or becoming uneven.
6.Drying and testing :
After printing is completed, the ink is cured through drying equipment, and finally the printing quality is checked one by one.
IV. Notes:
1.Environmental conditions : The printing environment needs to maintain appropriate temperature and humidity to avoid printing defects caused by static electricity or moisture.
2.Equipment maintenance : The screen plate and related equipment should be cleaned before and after printing to prevent ink residue from affecting subsequent use.
3.Quality control : During the printing process of each batch, random sampling is required to test the printing effect to ensure consistency.
4.Safety protection : During operation, be careful to prevent the inhalation of volatile ink and wear necessary protective equipment.
Through standardized operating procedures and strict quality control, screen printing of PE transparent ziplock bags can achieve high-quality Logo presentation and add brand value to corporate products.