Introduction of Fully Automatic Bottle Cap Pad Printing Machine
Introductin of Automatic Bottle Cap Pad Printer
The fully automatic bottle cap pad printer is a device designed for printing on the surface of bottle caps, and is widely used in beverage, medicine, cosmetics and other industries. This machine can achieve high-quality pattern printing on irregular surfaces such as plastic bottle caps through precise pad printing technology. Compared with traditional manual or semi-automatic equipment, the fully automatic bottle cap pad printer has high efficiency, high precision and high stability, which greatly improves production efficiency and reduces labor costs.
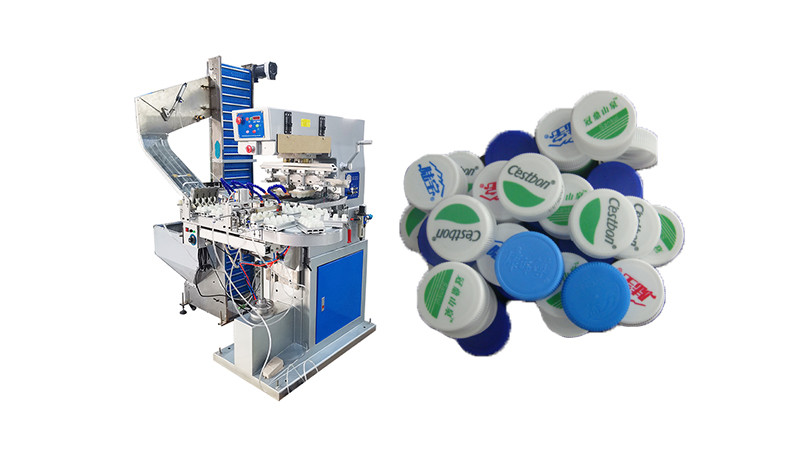
1. Advantages of the machine
1. Efficient automation: The fully automatic bottle cap pad printing machine adopts a PLC control system and is equipped with advanced sensors and automation devices. It can automatically complete a series of processes such as feeding, pad printing, and drying, reducing manual intervention and improving the automation level of the production line.
2. Precise printing: The machine uses a high-precision pad printing plate and ink transfer system to ensure that the pattern of each bottle cap is printed clearly and evenly with high color reproduction, meeting a variety of design requirements.
3. Save space: The equipment has a compact structure and occupies a small area, which is suitable for small and medium-sized enterprises. At the same time, automated operation reduces space waste and improves production efficiency.
4. Environmental protection and energy saving: Equipped with advanced ink management system to ensure efficient use of ink and reduce waste, while meeting environmental protection requirements and reducing the emission of harmful gases.
5. Easy operation: The human-machine interface is simple and intuitive, and the operator can easily adjust the machine parameters through the touch screen, which is convenient for operation and maintenance.
2. Operation process
1. Preparation: First, check whether all parts of the machine are intact and ensure that the bottle caps, inks, pad printing plates and other materials are ready.
2. Debug the machine: set parameters such as printing speed, printing pressure and drying time through the touch screen, and conduct trial printing to ensure that the printing effect meets the requirements.
3. Feeding and pad printing: Put the bottle caps into the automatic feeding system, and the bottle caps enter the pad printing area through the conveyor belt. The pattern on the pad printing plate is transferred to the surface of the bottle cap through the ink.
4. Drying and curing: After printing, the bottle cap passes through the drying system to ensure that the ink cures quickly to avoid blurring or falling off of the pattern.
5. Automatic discharging: The dried bottle caps are automatically transferred to the discharging area to complete the entire printing process.
3. Precautions
1. Regular cleaning: The ink transfer system, printing plate, scraper and other parts of the pad printer need to be cleaned regularly to ensure printing quality and extend the service life of the equipment.
2. Check the ink quality: Use ink suitable for the bottle cap material to avoid expired or substandard ink that affects the printing effect.
3. Adjust pressure and speed: Adjust the appropriate printing pressure and speed according to the material of the bottle cap and the complexity of the pattern to ensure the best printing effect.
4. Safe operation: Operators must wear appropriate protective equipment to ensure that no accidents occur during normal operation of the equipment.
The fully automatic bottle cap pad printing machine has become an indispensable and important equipment in modern production lines with its advantages of high efficiency, precision and environmental protection, and is suitable for printing needs of various bottle caps.