Screen printing – automation technology in the production of electronic ceramic products
Modern microelectronic packaging, especially electronic ceramic packaging, has higher and higher requirements for the printing graphic resolution and printing quality of the substrate, coupled with the miniaturization, lightweight, power, and metallization requirements of electronic devices, which promotes the development of electronic packaging technology in the direction of high integration and high packaging density, and requires smaller and smaller conductor lines and line spacing in the circuit, and higher and higher resolution.
In the above context, screen printing has become an extremely important process in the production process of electronic ceramic products, such as thick film ceramics (TFC), low-temperature co-fired ceramics (LTCC), high-temperature co-fired ceramics (HTCC), chip multilayer porcelain dielectric capacitors (MLCC), etc., and a large number of screen printing processes are used in the production process.
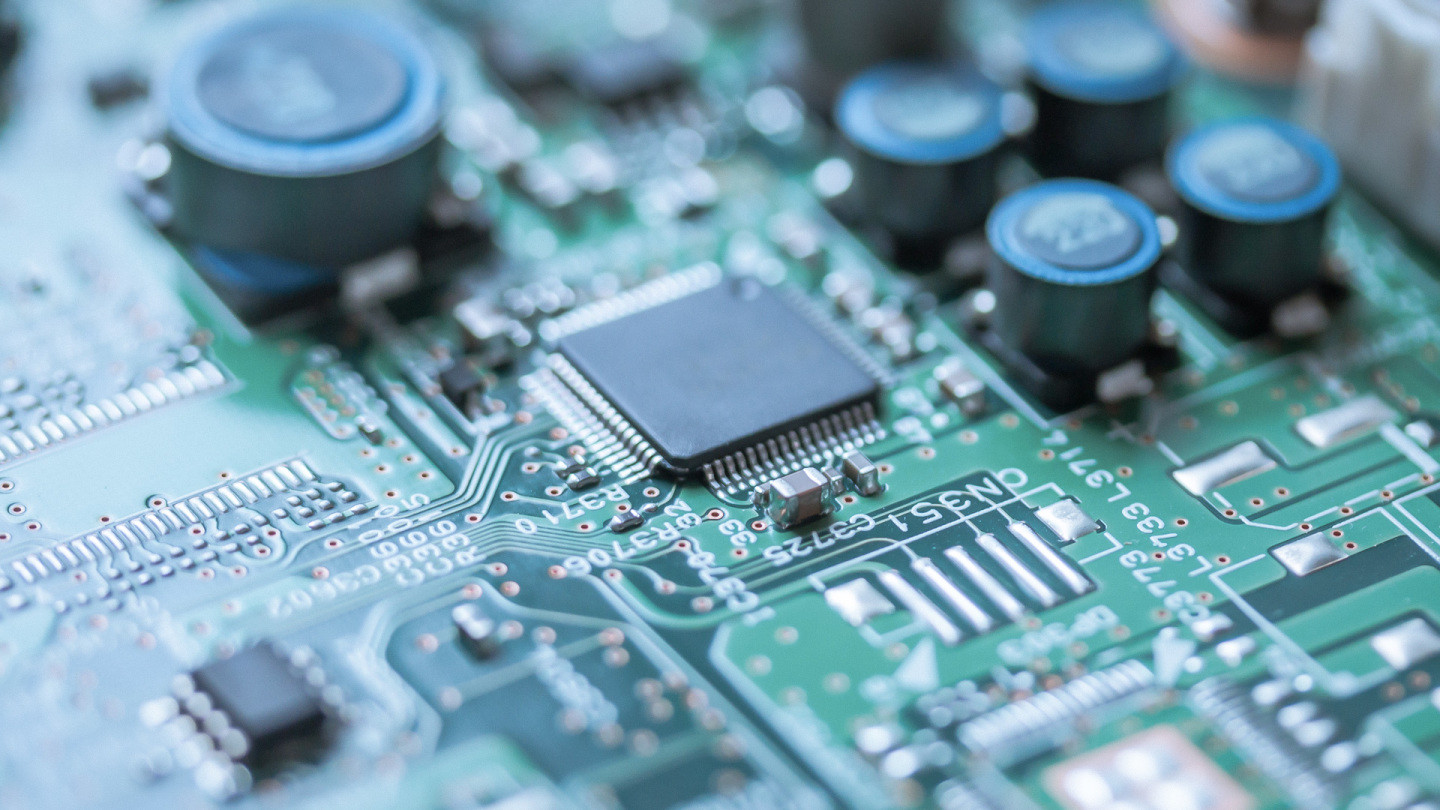
1. What is screen printing technology?
Screen printing is a very traditional printing method, which is widely used in China's electronics industry, ceramic decal industry, and textile printing and dyeing industry. The basic principle of this technology is that part of the mesh of the screen printing plate is able to pass through the paste, and the rest of the mesh is blocked, unable to penetrate the paste, forming a blank on the substrate.
In the field of electronics, it is used in the manufacture of printed circuit boards, thick film integrated circuits, solar cells, resistors, capacitors, piezoelectric elements, photosensitive elements, thermal components, liquid crystal display components, etc., and is adapted to various new materials and high-precision automation equipment in practice, which improves the process manufacturing level of today's screen printing technology.
2. Characteristics of the screen printing process
(1) It can be applied to the printing of different shapes, different areas and different materials, for example, it can be used for flat surfaces, and can also be used for concave and convex bodies with special shapes, and it is suitable for glass, ceramics, plastics and other materials.
(2) The screen printing layout is soft and elastic, so it can be printed not only on soft thin surfaces, but also on fragile and brittle objects.
(3) The thickness of the printing layer is easy to adjust, and the three-dimensional sense is strong.
(4) It is suitable for printing all kinds of different slurries.
(5) The cost of screen printing equipment is low, and it is easy to form large-scale production.
3. Application of screen printing technology in integrated circuits
Integrated circuits can be broadly divided into two categories: semiconductor integrated circuits and hybrid integrated circuits, which in turn can be divided into thin-film hybrid integrated circuits and thick-film integrated circuits. Among them, thin-film integrated circuits are manufactured using thin film technology using vacuum jetting method, and thick-film integrated circuits are manufactured using screen printing thick film technology.
Fig. Ceramic thick film circuit screen printing machine via Ebela printing equipment
The screen printing image of the integrated circuit is miniature, which requires high printing accuracy, so the printing press, printing plate, substrate (substrate), ink, etc. all need high precision, and the printing place must also maintain a constant temperature and remove dust.
4. Screen printing process materials in thick-film integrated circuits
1. Screen printing plate making:
1) Wire mesh:
One of the main materials, the commonly used nylon screen mesh and polyester wire mesh are not suitable for high-quality screen printing products due to factors such as large stretching, poor printing graphic accuracy, and difficult to control thickness uniformity. The stainless steel mesh has the characteristics of uniform wire diameter, consistent mesh thickness, small stretch and good ink passability, so the printed graphics are of high quality and wide adaptability, and are suitable for conductor printing in the electronics industry.
Parameters such as the number of meshes, wire diameter, and opening size of the screen have a great impact on the quality of screen printing.
2) Stretch net:
Generally, the screen frame is selected as an aluminum frame, and the stretching process directly affects the quality of plate making, and the quality of the stretching mesh is to control the tension.
When stretching the net, the wire mesh should have a certain tension, and the tension should be uniform. The tension of the mesh is too great, and it is easy to deform or tear the wire mesh. The tension of the stretch mesh is too small, the screen is soft, the printing is blurred, and the thickness of the film is thin. In the process of stretching the net, the tension meter should be used to measure the tension of the wire mesh at any time, and the force should be stopped when the standard tension is reached, so that the tension is transmitted evenly.
3) Photosensitive adhesive:
The main requirements of screen printing plate making for photosensitive adhesive materials are good plate-making performance, easy coating, definite photosensitive spectral range (ultraviolet ray), good developing performance and high resolution. The main components of photosensitive adhesives are film-forming agents, photosensitive agents and additives.
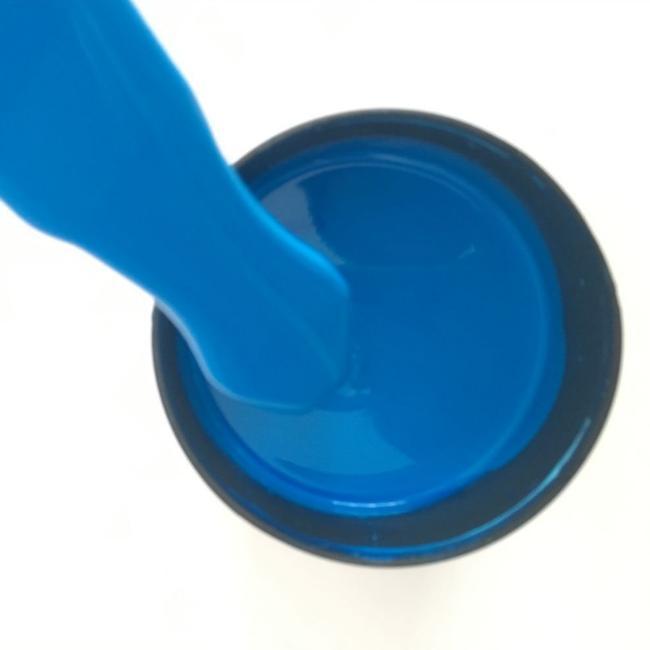
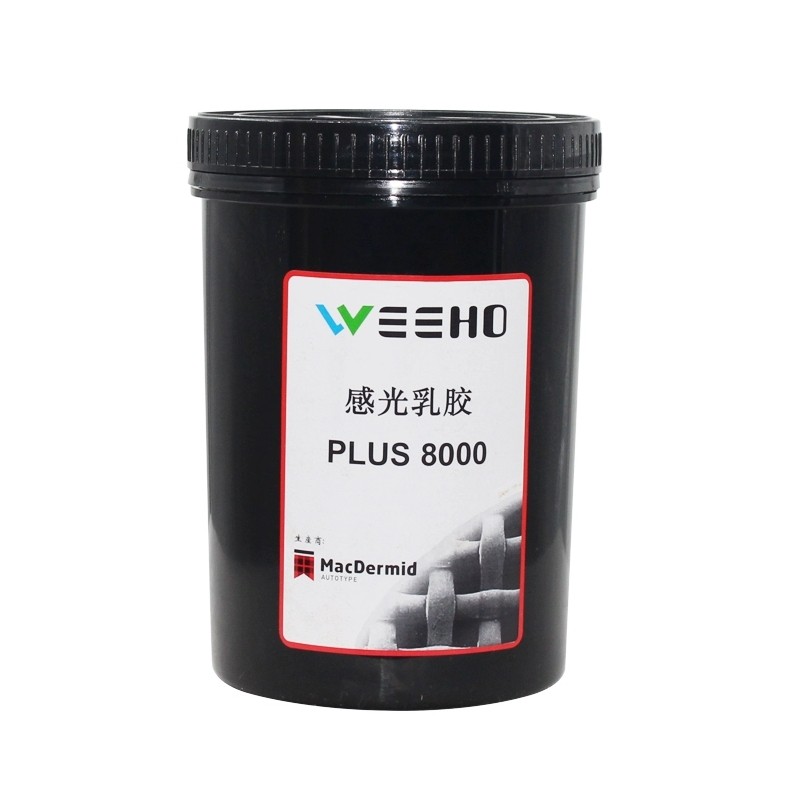
4) Scraper material:
The scraper material is generally polyurethane rubber or fluorinated rubber, and the hardness is Shore A70°~A80°. In addition, when choosing the shape and hardness of the scraper, you should consider what pattern you want to print on the board. In general, the blade of the scraper is 90° or 60°, and the angle of the scraper is 70°~75°.
2. Ceramic plate:
At present, the most mature ceramic substrate material is alumina ceramic substrate, which is a material with alumina (Al2O3) as the main body, which has good conductivity, mechanical strength and high temperature resistance. There are also ceramic substrates made of aluminum nitride, beryllium oxide, silicon carbide, boron nitride and other materials on the market.
3. Slurry:
There are three kinds of conductor paste, resistance paste and insulating paste, and the paste is generally composed of precious metals and low melting point glass. When making slurry, pay attention to the material, viscosity and expansion coefficient of the slurry. The paste used to print thick film circuits is composed of gold, silver, platinum, palladium, etc.
The above-mentioned metal powders are dispersed in an organic resin binder and modulated into a paste, which is then printed on a ceramic substrate by means of a screen printing plate. After firing at high temperatures, the organic resin binder is burned off, and what remains is almost pure precious metal, which is bonded to the substrate due to the action of vitreous. This film can be used as a base metal sheet for thick film lines, thick film resistors, thick film capacitors, and semiconductor integrated circuits.
5. Silk screen post-processing
For general printed circuit boards, conductor printing is carried out first, and then the resistor is repeatedly printed 2~3 times, and sometimes the printing of glass coating is carried out appropriately according to the situation, and the following processing or treatment is carried out after printing:
(1) Flattening process: After printing, the printed product will be placed for 5~7 minutes until the anilox disappears;
(2) Drying treatment: drying at a temperature of about 100 °C;
(3) Firing: Firing at a temperature of about 650~670 °C. This process is very important, so the furnace temperature should be adjusted at any time to maintain a temperature suitable for slurry sintering;
(4) Adjustment: Adjust the resistance value, generally by sandblasting to the circuit board or adjusting the resistor body with a laser;
(5) Encapsulation: It protects the internal components made of it.