How To Adjust Ink Layer Thickness and Uniformity in Screen Printing?
Methods for Adjusting Ink Layer Thickness and Uniformity in Screen Printing
1.Installing the squeegee
Take the squeegee strip and install it into the blade holder, check if the squeegee strip is installed evenly using the platform as the reference.
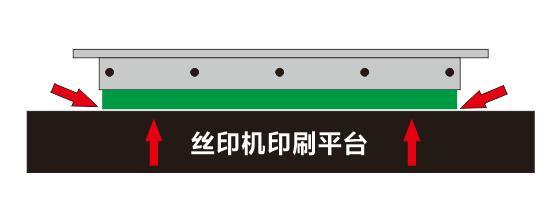
Figure 1.Check if the contact points between the squeegee and the platform are even.
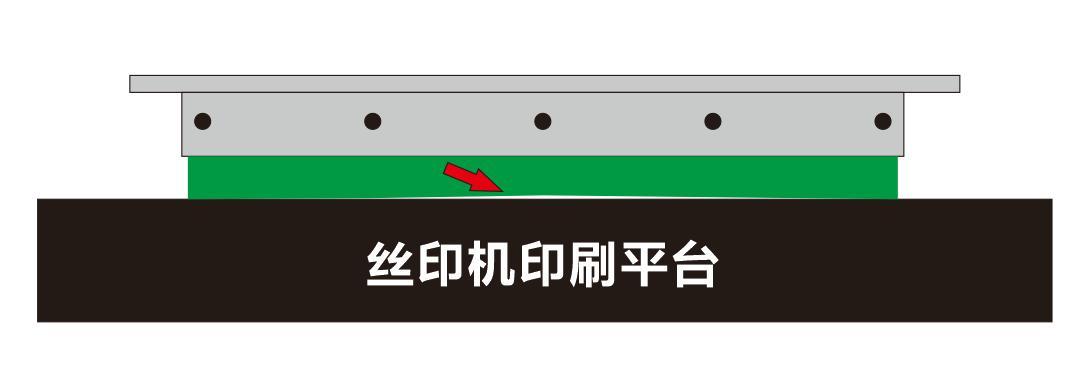
Figure 2.If there are visible gaps between the squeegee and the platform, it indicates that the platform is uneven or the squeegee strip is not installed correctly.
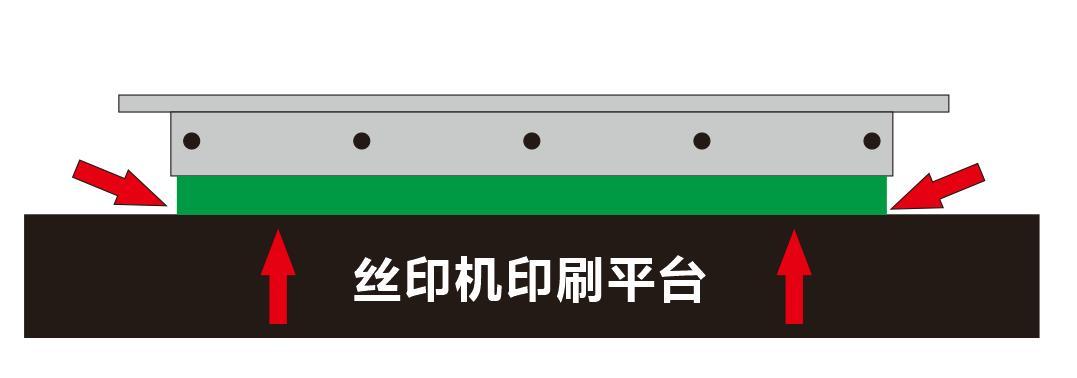
Figure 3.If there are no gaps, the platform and squeegee are level, and the squeegee is ready for use.
2.Installation and adjustment of scraper
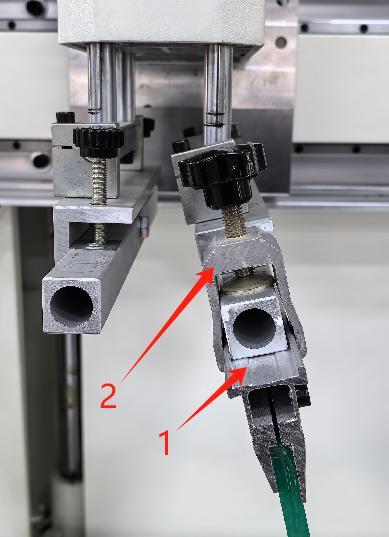
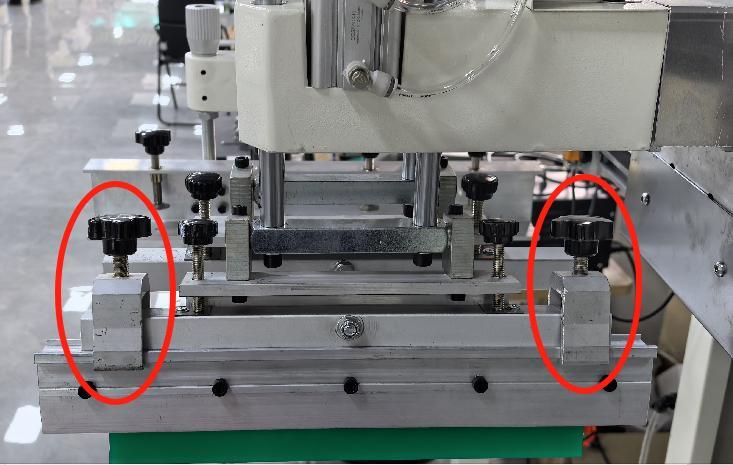
1.(Position 1)Insert the scraper horizontally into the holder, secure the scraper hooks on the both ends and tighten the star-shaped handle screws (position 2)

2.Loosen the two hex screws(red marked) to tilt the blade at a 30-35° angle, which is suitable for most printing applications.
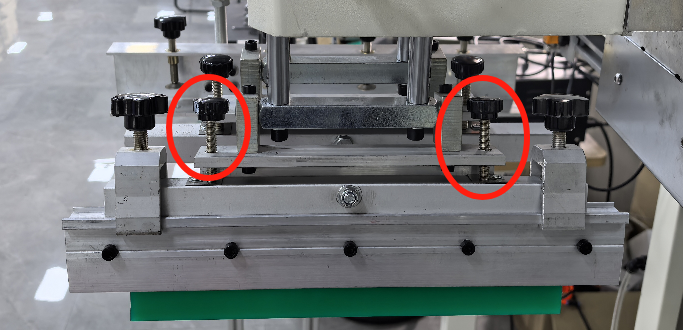
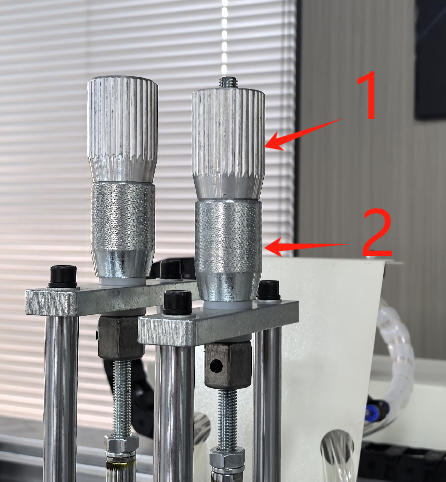
3.Loosen the two plastic handle screws marked.Operate the panel to perform the squeegee downward action(Scraper Switch).Turn and loosen the marked position 1 ccw then, use two fingers to hold position 2 and rotate it clockwise to adjust the downward stroke until it can no longer be turned with two-finger force.Confirm that the squeegee is now tightly pressed against the platform (fixture/product surface).
Then, use both hands to simultaneously tighten the two plastic handle screws clockwise.At this stage, the squeegee's parallel alignment with the platform (fixture) is basically completed.Fine-tune the tightness of the plastic handle screws to achieve optimal printing pressure during subsequent printing tests.
3.Installing the Screen Frame
Adjust the screen height to keep all four edges level with the worktable.
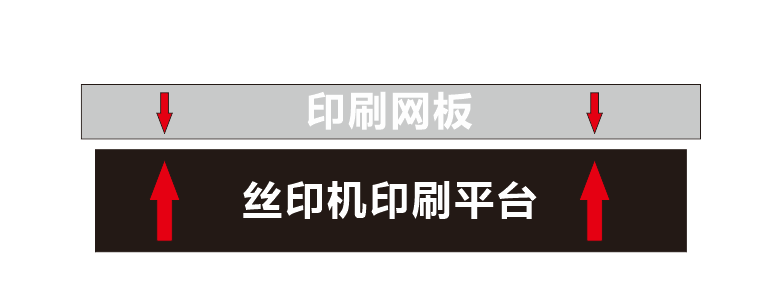
Figure 1.The screen frame is level if all edges are aligned with the worktable.
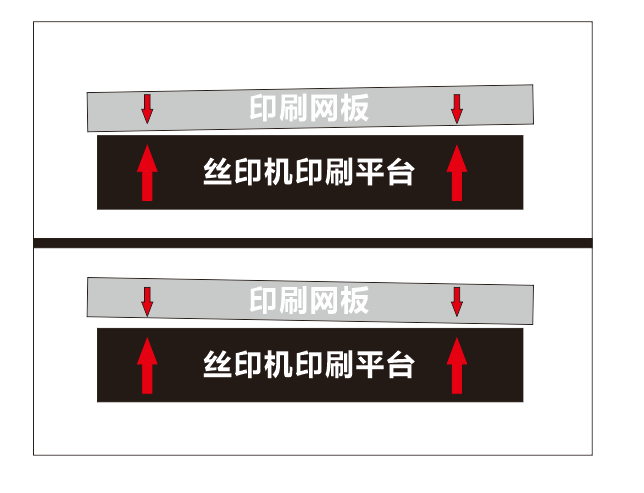
Figure 2.If the screen is tilted like the figure, follow the steps below to correct it:
2-1Adjusting the Left Clamp Arm Height
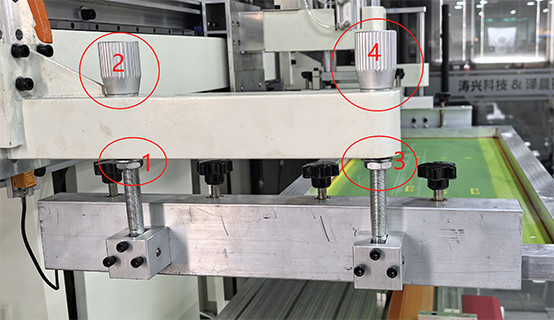
1.Loose the screw position 1, rotate potion 2 handle ( clockwise to raise the screen, ccw to down the screen) to raise or down the inner side screen.
2.Loose the screw position 3,rotate potion 4 handle( clockwise to raise the screen, ccw to down the screen) to raise or down the outer side screen.
3.Adjust both handles(position 2、4) simultaneously to raise or lower the entire left clamp arm.
2-2Adjusting the Right Clamp Arm Height
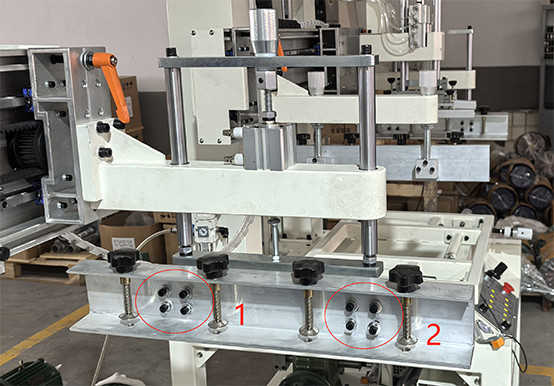
1.Loosen the 8 screws (Positions 1 and 2) to move the screen up or down, keeping it level with the worktable, tighten the screws to finish the leveling adjustment of the inner and outer right screen frame.
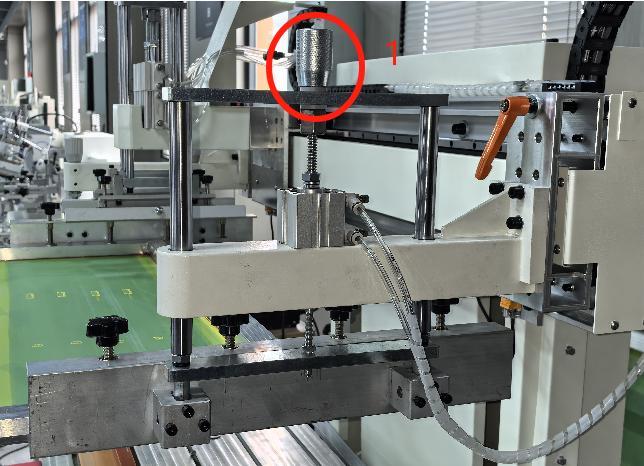
2.Rotate the position 1 handle to adjust the overall height of the right screen frame.(Clockwise ratate to down the screen frame, ccw to raise the screen frame)
4.Effect of Distance Between Screen and Product
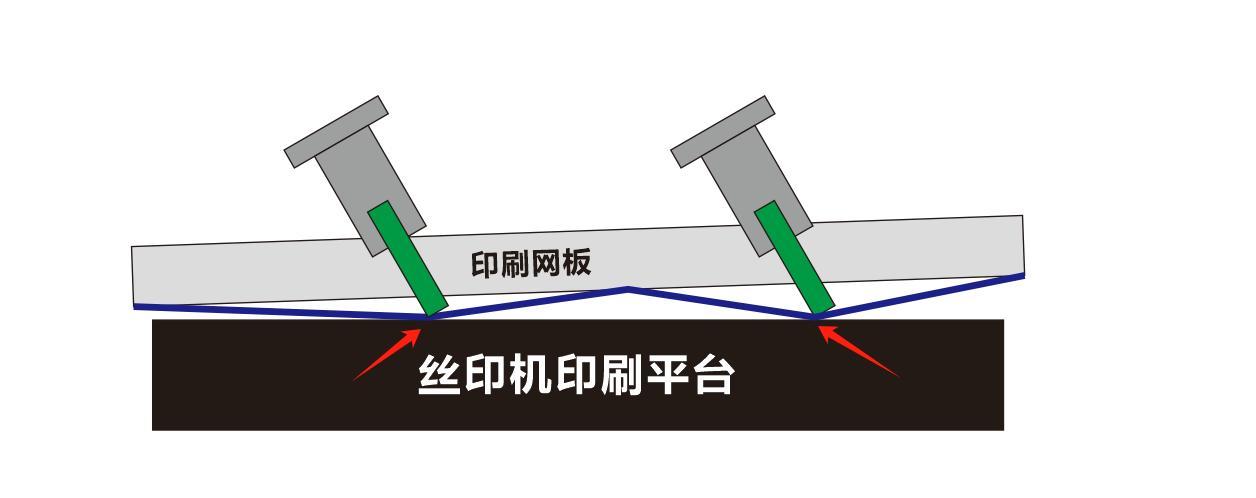
Based on a 5mm off-contact distance, when the off-contact distance exceeds 5mm, the squeegee encounters greater resistance during downward pressure, increasing the deformation angle of the squeegee blade and resulting in a thicker printed ink layer. Additionally, the varying downward displacement of the mesh can lead to changes in the pattern dimensions and misalignment in printing.
Note: The error value here varies with the height of the screen frame. The smaller the difference in off-contact height, the smaller the coating error in printing, and the higher the accuracy.
5.Influence of Mesh Count and Wire Diameter on Printing
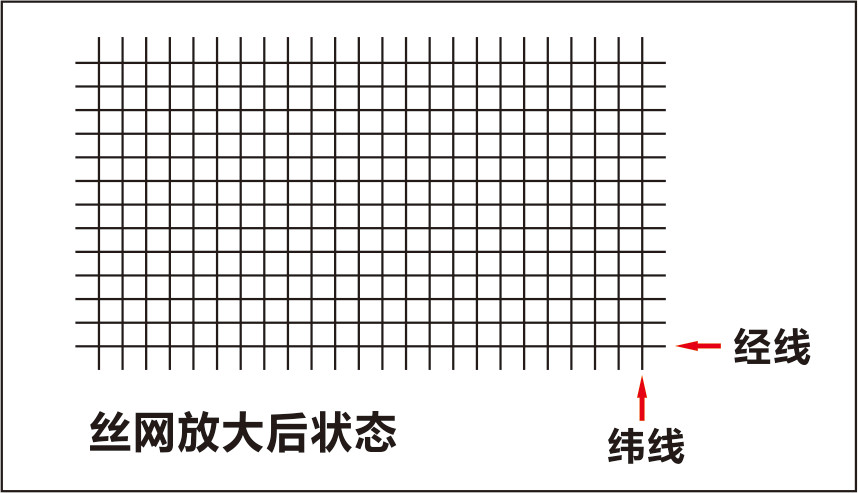
5.1.Composition of the Screen Mesh
As shown in the image, when the screen mesh is magnified, it can be observed that it is woven from horizontal and vertical threads, referred to as warp and weft threads.
5.2.How to choose the mesh count
Mesh count is an index used to measure the hole quantity of the screen mesh. It refers to the number of mesh openings uniformly distributed per inch (25.4mm) in length or width.
For example, a 50-mesh screen means there are 50 holes per inch, while a 100-mesh screen has 100 holes per inch. The higher the mesh count, the smaller and denser the holes, allowing finer particles or materials to pass through. Conversely, a lower mesh count means larger holes, allowing coarser particles or materials to pass through.
5.3.What are the other differences in screen meshes besides the mesh count
In addition to different mesh counts, screen meshes also differ in the thickness of the warp and weft threads. For the same 50-mesh screen, a mesh with thicker threads will have smaller hole openings, resulting in a reduced ink deposit and a thinner coating on the substrate. In contrast, a mesh with thinner threads will have larger hole openings, allowing more ink to pass through, resulting in a thicker coating on the substrate.
5.4.How emulsion thickness of screen mesh affect on the printing ink layer thickness?
The thicker the photosensitive emulsion, the thicker the printed coating layer will be. Additionally, screens with thicker warp and weft threads are more likely to produce thicker screen frames. Conversely, screens with thinner threads will result in relatively thinner screen frames.
6.Methods to adjust the coating thickness without changing the thickness of mesh count or emulsion.
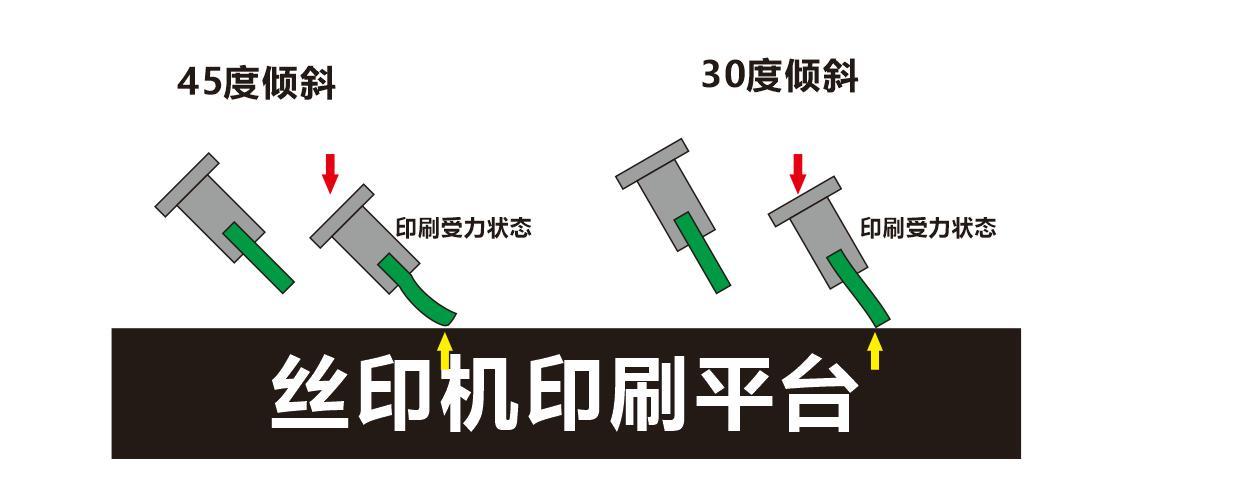
As shown in the image, the different angles of the squeegee affect the printing process. When the squeegee is subjected to downward pressure, the squeegee blade deforms, causing a change in the contact position with the product.
With a 30-degree tilt, the squeegee blade still makes contact with the product along the blade edge. The blade edge provides good support and high hardness, which allows it to scrape off excess ink during the printing process. This reduces the amount of ink passing through the mesh, resulting in a thinner coating. The printing of high-definition, fine-line patterns will achieve better results.
At a 45-degree angle, the squeegee deforms significantly, and the contact between the squeegee and the product shifts to the side flat surface of the blade. In this state, the squeegee's support and hardness decrease, and the contact area with the product becomes larger. As a result, it cannot quickly scrape off the excess ink, causing more ink to pass through the mesh and deposit on the product surface, resulting in a thicker coating. However, this condition also leads to an uneven coating thickness across the entire surface.